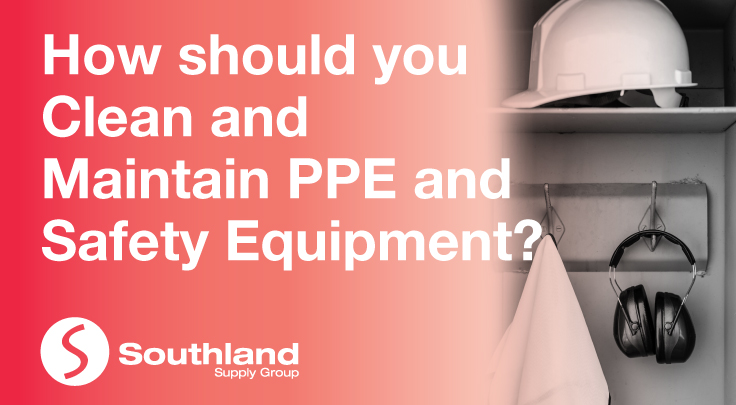
In many industries, employees work in potentially hazardous environments. Therefore, personal protective equipment (PPE) is essential for their safety. In some cases, it’s the only thing standing between them and a serious injury.
PPE is only effective when it is clean and properly maintained. Depending on the equipment and the industry, cleaning and maintaining requires a different approach.
Why Is Proper Maintenance of PPE and Safety Equipment Essential?
Taking good care of your PPE will prolong its lifespan. Damaged equipment can’t do its job properly, and it often puts employees at greater risk because they believe they’re protected when, in fact, the damage has rendered the PPE ineffective. By cleaning your equipment, storing it in a proper PPE storage cabinet, and inspecting it for damage before you use it, you’ll stay safer and be able to use that equipment for longer before you need a replacement.
Best Practice Cleaning Personal Safety Equipment
Check the manufacturer's instructions: Before you start cleaning or disinfecting your PPE, it is vital to check the manufacturer's instructions. This will provide specific details about the materials used to construct the equipment, which can affect how it should be cleaned.
Disassemble the Safety Equipment: If possible, disassemble the equipment before cleaning. This way, it’s easier to clean all the individual components of the equipment. Make sure to use the appropriate tools to disassemble the equipment to make sure not to damage any parts.
Pre-clean the Equipment: Before disinfecting the equipment, pre-cleaning is important. Use a soft brush or cloth and water to clean the equipment thoroughly. Make sure to remove all visible dirt, debris, and organic matter. For PPE like safety glasses, you can use lens cleaning fluid and lens cleaning tissues for pre-cleaning.
Disinfect the Equipment: After pre-cleaning, disinfecting the equipment using an appropriate disinfectant is vital. Follow the manufacturer's instructions for the correct disinfectant and make sure to cover all surfaces.
Rinse and Dry the Safety Equipment: After disinfecting the equipment, rinse it thoroughly with clean water to remove any residual disinfectant. Then allow the equipment to air dries completely before using it again.
Store the Equipment: After cleaning and disinfecting, store the equipment in a clean, dry, and well-ventilated area. Store the equipment in a way that prevents contamination from dust, dirt, or other contaminants. It is also worth it to consider using a proper PPE storage cabinet.
How Often Should Equipment be Cleaned?
It is always a good practice to keep your equipment clean. Consider making regular cleaning of your gear part of your process by adding it to your inspection forms or checklists. Because of the need to let equipment dry, it may make the most sense to make your policy to clean the equipment after using it each time, ensuring that clean gear is always available for the next time it needs to be used.
In conclusion, cleaning and maintaining PPE and other safety equipment is critical to ensuring their effectiveness and preventing the spread of infectious diseases and other contaminants. It is essential to follow the manufacturer's instructions, pre-clean the equipment, disinfect using an approved disinfectant, rinse and dry the equipment, and store it properly. By following these steps, you can help keep yourself and others safe in the workplace.