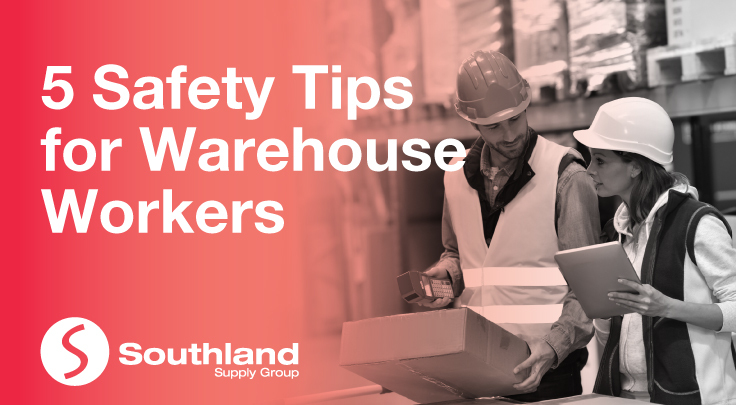
Working in a warehouse has a number of health and safety risks. If they are not controlled, your warehouse may face issues such as high employee turnover, underperforming employees, injuries and illnesses, lost working days, legal issues, and, at worst, fatalities.
As an employer, you are legally required to implement and maintain warehouse safety procedures. These safety procedures must protect workers from warehouse hazards and ensure that they can carry out work activities safely.
Moreover, you should also focus on promoting thorough warehouse safety procedures for reasons beyond compliance. Maintaining good safety practices shows that you value your staff’s well-being and want to do things right, which boosts motivation and increases trust in your leadership.
Here are 5 tips for effectively improving safety in your warehouses:
1. Wear Protective Gear
Examples of PPE may include safety glasses or goggles, hard hats, fire-resistant clothing, safety boots, earplugs, and work gloves. Generally warehouse staff will be allocated protective gear upon hire, however, other contractors and those working through agencies or on-demand staffing platforms may be expected to supply their own. It is important to know who is responsible, as miscommunication can lead to employees working without adequate protection.
2. Use Signage to Communicate Warehouse Safety Rules
Installing safety signs in strategic areas should be on the top of your to-do list. Some signs that may be required in your warehouse include:
- Flammable materials sign
- Hazardous chemicals sign
- Risk of fall sign
- Hard hat-only zones
- Look out for moving vehicles sign
Warehouses can get busy and hectic, and employees may not be able to hear each other over the constant noise of forklifts, trucks, and other equipment. While some things may seem obvious to seasoned staff, remember that there are often new people on the floor who aren’t as experienced. It can help to give them easy-to-read visual cues, so everyone is on the same page with safety awareness. Inspect safety signs on a regular basis and put that task on your warehouse safety inspection checklist to ensure that all warehouse safety signs are legible and hanging properly.
3. Follow proper lifting techniques
Improper lifting, repetitive motion or poor design of operations can lead to musculoskeletal disorders in workers. It is recommended to use powered equipment instead of requiring a manual lift for heavy materials. It is also important to ensure overheard lighting is adequate for the task and keep floors clean and free of slip and trip hazards.
4. Keep areas clean and organised
It is essential that floors are kept free of slip and trip hazards. It is also important that all staff understand the importance of good housekeeping. There should be regular checks on any stray cords, liquids, accumulated debris, cracks, and pits on the floor. These can cause severe injuries to employees and damage valuable machinery and cargo.
5. Get to know all emergency procedures
All warehouse workers must be thoroughly trained on important safety protocols like evacuation procedures, hazard communication, fire safety procedures, and so on.
Creating a safe and productive warehouse environment always starts with a culture of safety. This culture must be reinforced by the managers at all levels, especially executives and owners.
As an employer, you should always remember that safe employees are more productive and more likely to remain loyal to the company. If employers take care of their employees, their employees will take care of their jobs.
As a leader in providing high-quality protective gear and safety equipment, Southland offers a wide range of warehouse safety equipment to help you keep safe at work. Browse our range online or get in touch with us at 1800 77 22 91.